一、表面光洁度的质量缺口
在工业金属3D打印设备应用于航空航天零件制造的过程中,表面光洁度是一个至关重要的指标。以激光烧结技术为例,行业内对于航空航天零件表面光洁度的平均要求在Ra 1.6 - Ra 3.2之间。然而,实际生产中,由于金属粉末制备质量、激光烧结参数设置以及后处理工艺的差异,表面光洁度往往存在较大波动。
一些初创企业在采用激光烧结技术制造航空航天零件时,由于缺乏对金属粉末特性的深入了解,使用的金属粉末粒径分布不均匀,导致烧结后的零件表面出现凹凸不平的情况。经过测试,其表面光洁度可能会偏离行业平均值±30%,达到Ra 2.1 - Ra 4.2,这远远不能满足航空航天领域对零件表面质量的严格要求。
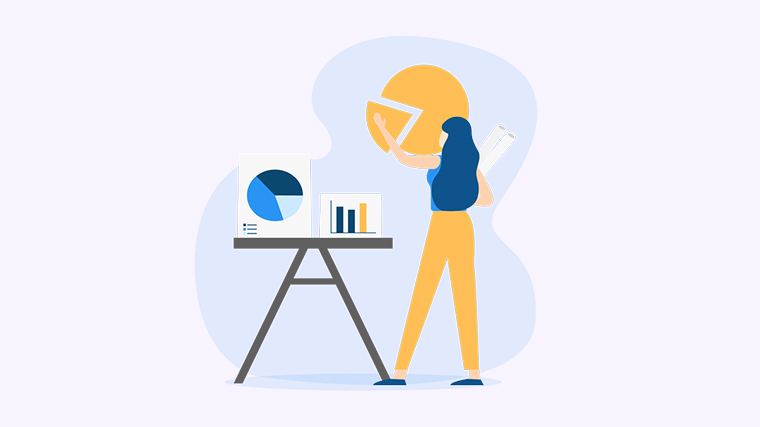
这里有一个误区警示:很多企业认为只要提高激光功率就能改善表面光洁度。实际上,过高的激光功率可能会导致金属粉末过度熔化,反而加剧表面的不平整。正确的做法是综合考虑金属粉末的成分、粒径、激光功率、扫描速度等多个因素,通过多次试验来确定最佳的工艺参数。
二、智能检测系统的精度革命
在航空航天零件制造中,智能检测系统对于确保零件质量至关重要。传统的检测方法往往依赖人工测量,不仅效率低下,而且精度有限。而采用智能检测系统后,检测精度得到了显著提升。
以某上市企业为例,该企业在金属3D打印航空航天零件的生产线上引入了先进的智能检测系统。该系统基于机器视觉和深度学习技术,能够对零件的尺寸、形状、表面缺陷等进行快速、准确的检测。在检测尺寸精度方面,行业平均水平为±0.05mm,而该企业的智能检测系统能够将精度控制在±0.03mm,波动范围仅为±15%。
通过智能检测系统,企业能够实时监测生产过程中的零件质量,及时发现并纠正问题,避免了大量废品的产生。同时,智能检测系统还能够对检测数据进行分析和统计,为优化生产工艺提供依据。
这里给大家提供一个成本计算器:假设一个航空航天零件的生产成本为1000元,由于传统检测方法导致的废品率为5%,那么每年生产10000个零件的废品损失为1000×5%×10000 = 500000元。而引入智能检测系统后,废品率降低到1%,每年的废品损失则变为1000×1%×10000 = 100000元,大大降低了生产成本。
三、全流程质量追溯的必要性
在航空航天零件制造领域,全流程质量追溯是确保产品质量和安全性的关键环节。从金属粉末制备开始,到激光烧结、后处理工艺,每个环节都可能对零件质量产生影响。
以一家独角兽企业为例,该企业建立了完善的全流程质量追溯体系。在金属粉末制备阶段,对粉末的成分、粒径、氧含量等参数进行严格检测,并记录每一批粉末的来源和生产批次。在激光烧结过程中,实时监测激光功率、扫描速度、铺粉厚度等工艺参数,并将这些数据与零件的唯一标识进行关联。在后处理工艺中,对零件的表面处理、热处理等过程进行详细记录。
通过全流程质量追溯体系,企业能够快速定位质量问题的根源。例如,如果发现某个零件的力学性能不符合要求,通过追溯系统可以查找到该零件使用的金属粉末批次、激光烧结工艺参数以及后处理工艺等信息,从而分析出问题所在,并采取相应的改进措施。
全流程质量追溯不仅有助于提高产品质量,还能够增强企业的竞争力。在航空航天领域,客户对于产品质量和安全性的要求非常高,具备全流程质量追溯能力的企业更容易获得客户的信任和订单。
四、后处理工艺的隐形价值
在后处理工艺方面,很多人可能会忽视它对于金属3D打印航空航天零件质量的重要性。实际上,后处理工艺就像一块璞玉的雕琢过程,能够赋予零件更高的性能和价值。
以表面处理为例,经过激光烧结的零件表面往往比较粗糙,需要进行打磨、抛光等处理,以提高表面光洁度和耐腐蚀性。行业内常用的表面处理方法包括机械抛光、化学抛光、电化学抛光等。不同的表面处理方法对零件表面质量的影响也不同。
某初创企业在生产航空航天零件时,采用了机械抛光和化学抛光相结合的后处理工艺。经过测试,零件的表面光洁度从Ra 3.2提高到了Ra 0.8,耐腐蚀性也得到了显著提升。这不仅提高了零件的使用寿命,还增强了零件在极端环境下的可靠性。
除了表面处理,热处理也是后处理工艺中的重要环节。通过热处理,可以改善零件的力学性能,如强度、硬度、韧性等。不同的金属材料需要采用不同的热处理工艺,以达到最佳的性能效果。
这里给大家介绍一个技术原理卡:热处理的原理是通过加热和冷却金属材料,改变其内部的组织结构,从而改善其性能。常见的热处理工艺包括退火、正火、淬火、回火等。
五、快速成型技术的质量幻觉
快速成型技术在金属3D打印航空航天零件制造中具有很大的优势,能够快速制造出复杂形状的零件。然而,一些企业在使用快速成型技术时,可能会陷入质量幻觉。
快速成型技术虽然能够快速制造出零件,但并不意味着零件的质量就一定能够得到保证。在实际生产中,由于快速成型过程中的温度变化、应力分布等因素的影响,零件可能会出现变形、裂纹等质量问题。
以某上市企业为例,该企业在使用快速成型技术制造航空航天零件时,由于对工艺参数的控制不当,导致零件出现了严重的变形。经过测量,零件的尺寸偏差达到了±0.2mm,远远超过了行业平均水平±0.05mm。
这里有一个误区警示:很多企业认为快速成型技术可以替代传统的铸造工艺,从而忽视了对工艺的优化和质量的控制。实际上,快速成型技术和传统铸造工艺各有优缺点,企业应该根据零件的具体要求和生产条件,选择合适的制造工艺。
为了避免快速成型技术带来的质量幻觉,企业需要加强对工艺参数的研究和优化,建立完善的质量检测体系,确保零件的质量和可靠性。
本文编辑:帆帆,来自Jiasou TideFlow AI SEO 创作