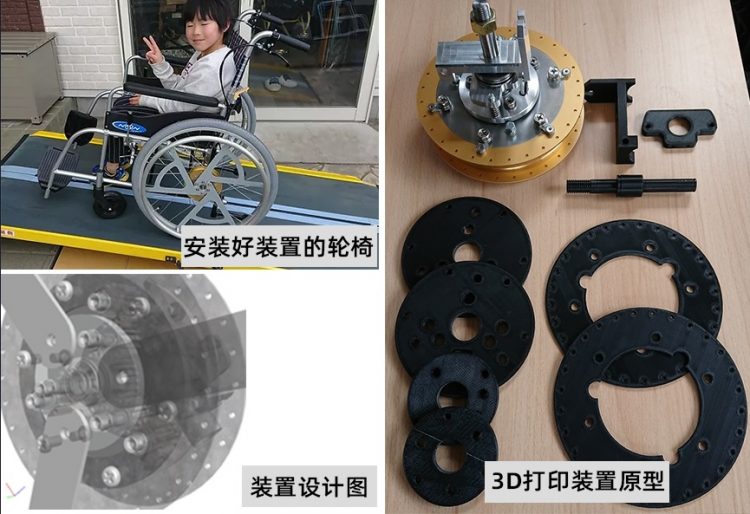
图 | Mon-Chan设计的防回滑装置
在引进Raise3D 3D打印机进行生产后,Mon-Chan可以灵活的根据客户需求去定制康复器械,以更低的成本、更快的生产时间去做个性化服务。小型制造企业的挑战
与快消品或者高端市场不同,Mon-Chan的市场更分散,占有率小,利润也有限。这样的情况限制了Mon-Chan的生产力以及规模。 康复器械,如轮椅,通常需要根据病患的自身情况进行定制。在进行定制化服务时,无论对于消费者还是制造商来说,都将面临较高的成本。而对于Mon-Chan这样小型的制造商,高昂的制作成本是个很大的挑战。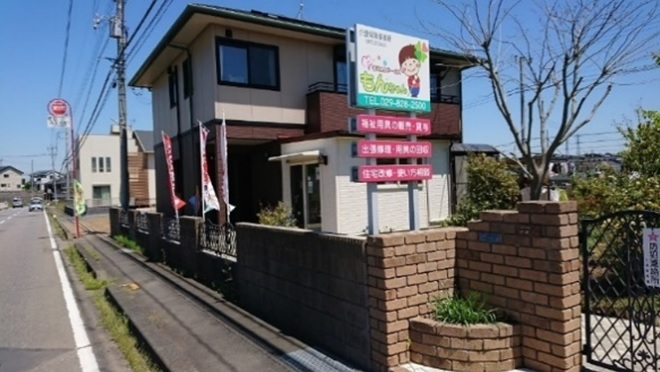
图 | Mon-Chan公司
不同于拥有工厂的大型制造商,Mon-Chan只是一间生产技术有限的小型企业。在过去的产品开发阶段,将原型制造外包出去是Mon-Chan唯一的选择。而在这个过程重,将会产生漫长的生产时间以及高昂的服务成本。数字化生产降低生产成本
为了降低生产成本以及更好的为客户提供定制化的服务,Mon-Chan采购了Raise3D 3D打印机,通过自主进行数字化生产,摆脱了对生产供应商的依赖,降低了生产以及时间成本,同时还降低了小企业规模运营的难度。 自决定改变生产方式后,Mon-Chan引进了一套完整的数字化生产的解决方案,包括3D扫描仪以及CAD软件。 正如他们在制作轮椅脚踏板时一样:Mon-Chan的设计师会先使用3D扫描仪对其库存中的标准零件进行扫描成型,然后再根据客户的需求,对3D模型进行定制化设计。在模型完成后,只需将其导入切片软件ideaMaker,选择好预设的打印参数模板,便可以快速完成切片工作。结尾,只需要将模型导入进打印机里,便可以进行定制化脚踏板的生产。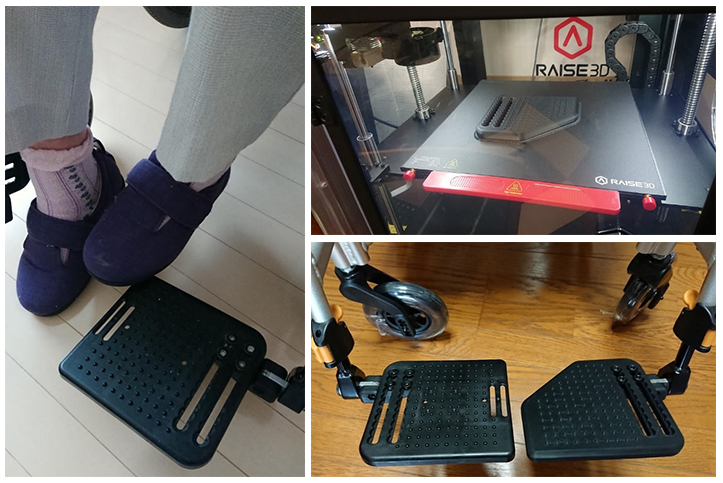
图 | Mon-Chan使用3D打印机为患定制轮椅脚踏板
这样数字化的生产模式,具有更高的灵活性,并且可以随时对模型进行修改。 在引进3D打印技术进行后,Mon-Chan在产品研发阶段,实现了自主生产设计原型。和以前依靠供应商生产的模式相比,Mon-Chan的开发周期和总成本分别减少了50%以及33%。 有了Raise3D 3D打印机后,设计师可以在数小时内制作多个版本的设计原型,并和工程师及时进行交流,检测原型设计的合理性或者交换修改意见,大力的减少了研发时间,也进一步加快了产品的制作时间。高效智能的切片软件
在进行3D打印时,Raise3D自主研发的切片软件ideaMaker为Mon-Chan提供了丰富的打印参数模板,设计师可以利用这些参数对模型进行设置,如:填充率、填充结构、层高等。当设计师想要设置打印零件的机械性能时,可以直接在ideaMaker对模型结果的进行设置而无需重新绘制模型。
图 | Mon-Chan利用ideaMaker设置零件内部填充
兼容多种耗材
在制作零件成品时,Mon-Chan通常会使用具有优秀的强度和抗冲击性的PC以及ABS等3D打印耗材,这样在制作一些如轮椅模块等承重零件时,可以确保零部件坚固且耐冲击。Raise3D的FFF 3D打印机可兼容多种耗材,可以灵活的适应Mon-Chan对不同零件的结构或功能要求。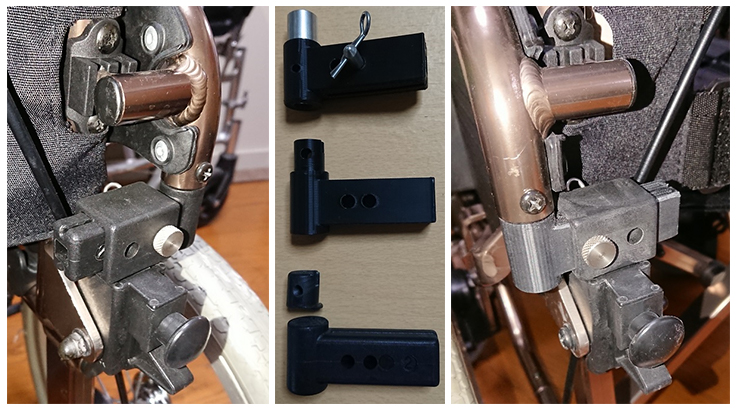
图 | 用3D打印修复10年前已停产的轮椅位置调节零件
原始零件(左)
打印的零件成品(中)
安装好的3D打印零件(右)