3D打印助力SpaceX航天部件翻修工作
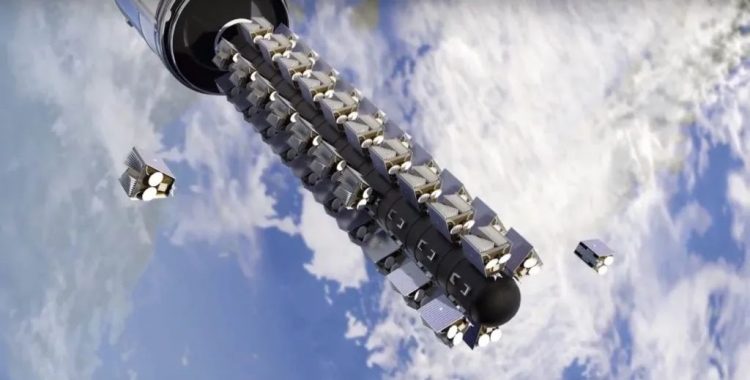

图 | Raise3D支持的夹具使用材料种类十分丰富
多项材料的选择满足了不同的工业客户的需求,尽管都是顶尖的工业客户,但根据行业或者使用场景而言,每一家企业对于材料的使用偏好也会有所不同。如Tesla偏好使用PETG材料,相较于一般打印使用的PLA或者ABS材料,PETG除了较易打印之外,还具有一定的韧性,在夹具装配时不会刮伤车漆表面,并且对于一般的汽车用油,清洁剂、肥皂液等具有一定的耐化学性能。 而波音公司则更多地使用Raise3D的设备打印通用的PLA材料。PLA(聚乳酸) 是一种生物基热塑性高分子材料,具有优异的生物可降解性,是较为常用的3D打印材料。它除了可以满足超大尺寸零件打印的同时,材料价格还非常便宜(每公斤仅20-30美元),并且拥有鲜艳的各种颜色选择,波音公司通常选择橙色、黄色或者鲜绿等亮眼的颜色,以区别不同的定位体系,这对于飞机装配定位的准确性和快速辨认非常有帮助。用户案例
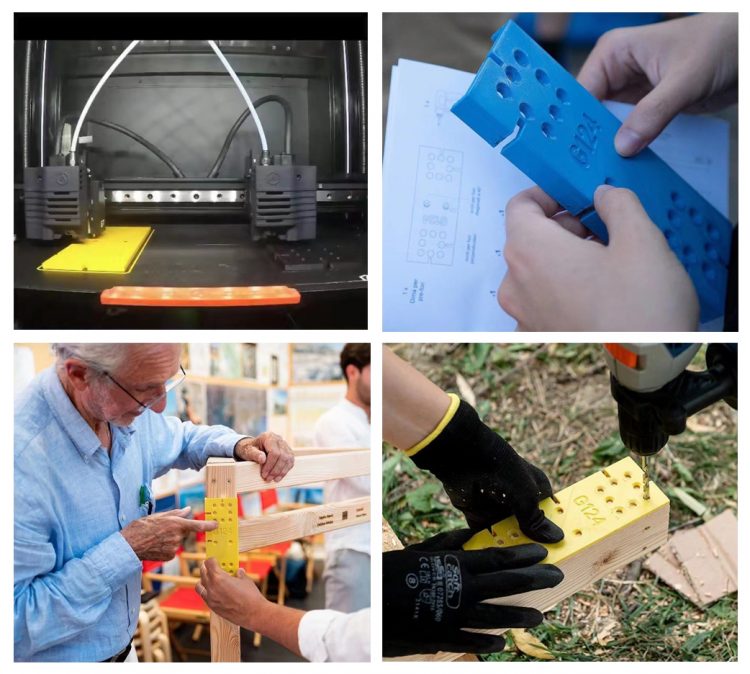
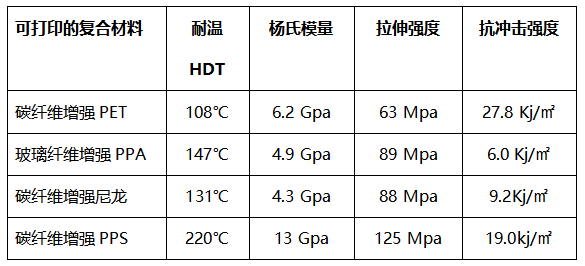
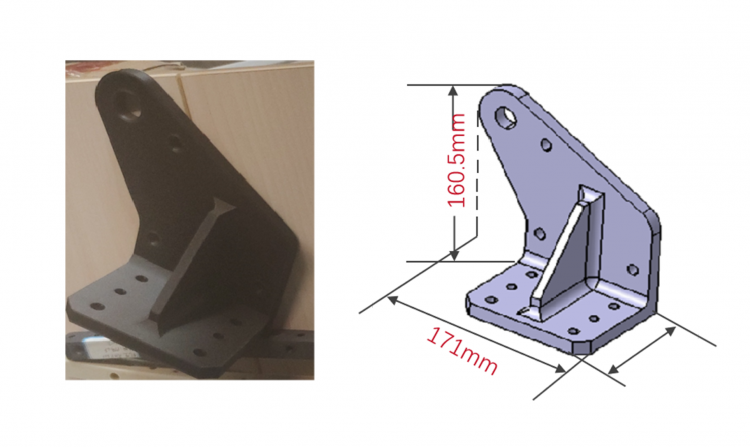
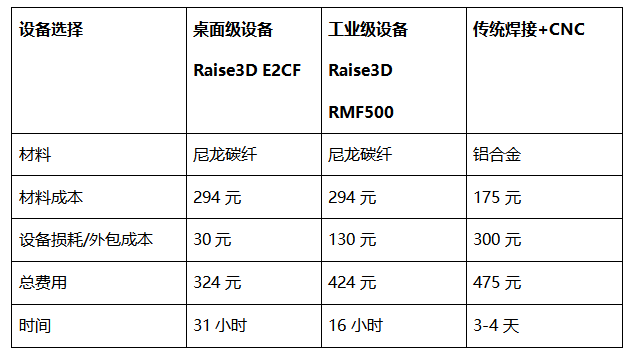